Modifying an edge trimming machine
The problem
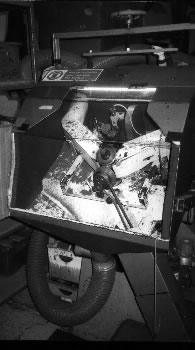
In shoe manufacture, sole forming leaves excess material at the edges which must be removed by holding each shoe against a high-speed rotating blade.
Machines traditionally designed for this purpose consist of a cutting head located inside a five-sided metal box. Operators get at the blades through an open sixth side, with the off-cut flashings either falling to the floor or being removed by a dust extraction system at the rear. The open front of the machine gives little acoustic protection for the operators and A-weighted noise levels can exceed 90 dB. The main source is thought to be the central spindle rotating at high speeds, generating a high-frequency tone.
The solution
One company fitted a simple system to each of their edge trimming machines by lining the inside of the machine casing with a 50 mm thick foam slab. This absorption restricted the build-up of reverberant sound energy inside the machine.
Each machine was also fitted with a 'half-height' clear polycarbonate plastic screen at the front, hinged along the top edge to enable it to be lifted clear, giving full access to the space inside. During operation, the screen could be lowered to give partial cover at the front, leaving a gap for the operator to reach in with the shoe. The treatment has proved to be a good compromise between screening direct sound radiation and maintaining efficient and safe operation.
The cost
About £50 per machine. (1995)
The result
A noise reduction of about 5 dB.
Source
Photographs courtesy of Clarks International.